Optical Coatings
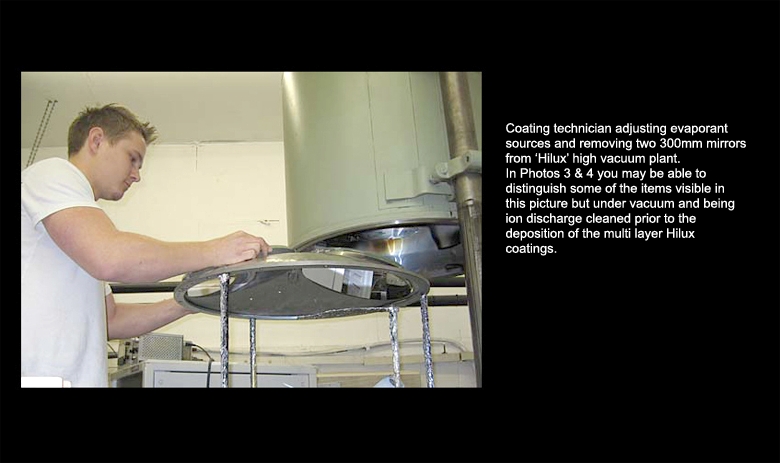
Hilux Enhanced Aluminium mirror coatings
Light is the most valuable commodity in telescopes but, all too often it is wasted unnecessarily. As an analogy, high quality optics are comparable to a formula one racing engine. The design is of great importance but, the attention to detail, especially any detail which can improve the power output of the engine is adopted and applied. To achieve all that horse power from a relatively small engine is only possible by applying skills, experience, quality materials, excellent design and innovation. We incorporated all these into Hilux coatings. We wanted to offer you the highest output possible from your telescope, we think we have achieved it. Having said that we do not sit back and relax thinking nothing else can be done. Development work on coatings is an ongoing programme within Orion Optics and when new developments are available to us, we pass them on to you.
We have developed and introduced, along with one of the UK’s leading coating designers, a new aluminium coating with enhanced multi layered overcoats to increase the reflectivity of telescope mirrors to almost 97% over a wide range of the visible spectrum. All coatings are carried out in our own optical coating laboratory with newly installed computer controlled coating plants. This arrangement allows us to ensure we test every single coating we apply for optimal performance.
What actually is Hilux ?
It is a method of allowing considerably more of the light which your telescope collects being passed to your eye or camera. Typically a standard coated telescope mirror with a typical protective layer of Silicon Oxide will reflect around 87-89%. This does vary depending on the actual measurements carried out during coating, assuming the deposition is being monitored and not just literally guessed at. If you consider a Newtonian, Cassegrain, Dall Kirkham, Ritchey Chretien etc, they all usually have 2 reflective surfaces in use to form the image. This means that, as an average, 88% is reflected from the main mirror and passes to the secondary mirror which, then reflects 88% of that. In total, there is about 77% of the light that enters the telescope reaches the useful bits, your eye or your camera.
Hilux has a completely different set of numbers. Over a wide section of the visible spectrum, the light which your eye is most sensitive to and, the light which CCD cameras like, every surface to which Hilux is applied, reflects up to 97% of the light it receives. You can see a representative graph here.
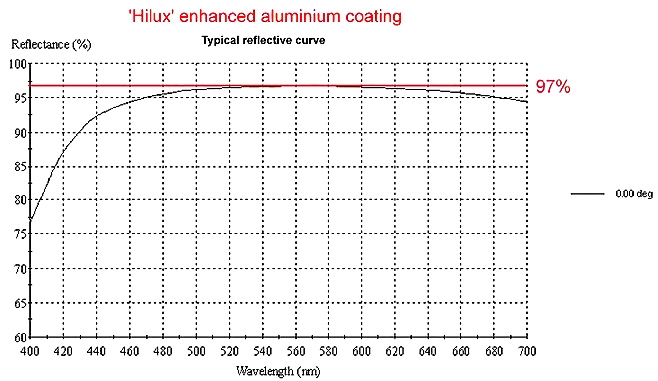
This light is then sent to the secondary mirror where again, up to 97% of the most important light needed by your eye or camera is reflected and captured by your retina or CCD chip. In the first example here showing what some standard coatings can produce, 77%, if you compare that with a figure produced by Hilux of up to 94%. By anyone’s standard, this is a remarkable and significant improvement in performance.
It is in fact, in brightness of image terms, 25% brighter image. Or, as an example, it’s like changing a 200mm telescope automatically into a 250mm telescope without having to do anything else at all.
How does Hilux actually work?
I will try to explain this as simply as possible because it is rather technical and a lot of mathematics involved, however, here goes. When light strikes a reflective coating on a mirror which has a single, protective silicon oxide overcoat, a few things happen. Some of the light is absorbed by the aluminium, some actually passes through the aluminium (around 0.5% or so) and some bounces around between the aluminium and the top surface of the overcoat. This bouncing is very complex as it happens a few times until the ‘bounced’ light is absorbed or passes out the back of the mirror or out from the front of the mirror, towards you. These losses and ‘bouncing’ cause a significant loss in the good, single reflected light which is the light you want. It can be improved on by careful monitoring of the coatings of the protective layer and the thickness and quality of the aluminium when it is being deposited but, at the end of the day, there is always a significant loss from each surface. Hilux avoids most of these faults. It still looses around 0.5% which passes through the aluminium and a smaller amount which is absorbed. Where it gains enormously though is avoiding considerably, this ‘bouncing effect’ by having the light pass through alternate layers of metallic dioxides of Silica and Titanium. These materials are deposited on top of the aluminium in precisely measured thicknesses to achieve the ‘prescription’ which gives Hilux it’s distinctive reflection graph above.
Are the elliptical secondary mirrors coated the same way with Hilux? No, they are not. The secondary mirrors in our ODK telescopes are as are any customised Cassegrain design we make but elliptical secondary mirrors undergo a different process. To be pedantic, the process really is only partly different. The aluminium layer is the same, the layers applied are exactly the same dioxides and the same order of application but, there is one massive difference which don’t know of any other manufacturer considers.
When we calculate the thicknesses of the Hilux individual layers it is based on the light striking the main mirror at virtually perpendicular or 90 degrees to the surface. This forces the light to pass though the Hilux layers once, reflect off the Aluminium and then pass backwards through the Hilux layers again. Very straightforward. In the case of an elliptical secondary mirror, the light strikes the mirror at 45 degrees, travels through the Hilux, comes off the aluminium and back out at 45 degrees through the Hilux. Here we have situation where the light is travelling considerably further through the Hilux layers because they are at 45 degrees to the light path, in effect, it is the square root of 2 further. If we coated secondary mirrors exactly the same as our primary mirrors, they would not work as well because the efficiency of the Hilux depends totally on it’s thicknesses of the dioxides the light has to travel to cancel out most of the ‘bouncing’ We have to coat the secondary mirrors with thinner layers of the Hilux materials to compensate for this,. In effect it is the thickness of the main mirror coatings divided by the square root of 2, or, about 30% less.
Will Hilux coatings last longer than standard coatings?
A resounding yes. Under the same conditions and use, Hilux coatings, because of the fantastic protection Hilux adds along with higher reflectivity, there is no reason Hilux coatings will not last 25 years or even longer. So, if you are considering re-coating your old telescope mirrors, regardless of from whom they came from, Hilux will give your mirror’s performance an extended life. We have had a small mirror outside in all weathers now since 2003 and if we wipe it carefully, it looks as good as the day we coated it. It has had, rain, snow, hail, everything the elements could throw at it. We don’t recommend that you do this though.
Does Hilux coating change the overall surface accuracy of the mirror?
Not at all. We are asked this question nearly every week because some customers are worried, especially those having their older mirrors recoated, that the Hilux will change the shape and performance of their mirror. Let me assure you, it won’t. To ensure this, every month we carry out maintenance coatings in our vacuum plant. We place microscope slides inside the chamber where the mirrors are coated and they are positioned at varying distances from centre to edge. We then carry out a test firing with only 10% of the aluminium we normally evaporate onto the mirror. This gives us what people term a ‘Two way mirror’. We then measure with out photospectrometer exactly how much light passes through the slide. If there is more than a few percent difference, we adjust the thermal evaporation sources in the vacuum chamber and test again. This ensures all mirrors are then coated evenly regardless of size or position in the vacuum plant.
Do you test the reflectivity of every mirror you coat?
No, we don’t test any of the paraboloids or any big mirrors, we do test the flat elliptical mirrors though. What we do in place of testing every mirror is, we fix inside the vacuum chamber, 2 microscope slides which are at the same distances from the thermal evaporation sources as the larger primary mirrors. We run the plant and then we test the slide’s reflectivity, already knowing the slide is an exact replica of the mirror’s coating because of monthly maintenance coating checks. We then record with graphs exactly how that batch of mirrors performed and keep records of this data and, keep the actual microscope slides. Because of the thousands involved here, we only retain details for up to about 3 years.
We looked at several ways of showing you exactly, or as near as possible, what actual difference in performance a set of Hilux coated mirrors would offer you compared to most standard, competitors coatings, This is not an easy task to actually perform without appearing to be significantly biased towards Hilux. Visually the eye will see easily the differences on Deep Sky objects, they are obvious but, because it is difficult to actually show this on a web page because deep sky visual observing is notoriously difficult to portray realistically, we looked at a different method and decided on a photograph of a medium length exposure of a deep sky, well known object.
We used an AG12 which has Hilux coatings and then took an image. We then carried out exactly the same exposure but with a reduction in the light vale of 25% i.e. standard optical coatings.
The results here are self explanatory for everyone to see.